Mari Kallioinen-Mänttäri, Dean of the Lappeenranta-Lahti University of Technology LUT, points out that the forest is a scarce resource, but almost unimaginably abundant in its diversity. For example, the side streams of production processes can be separated by biorefining to recover different compounds suitable for further processing.
“In addition to pulp fibre, wood biomass contains lignin and hemicellulose, which have significant processing value, especially if we can no longer use oil-based materials in the future.”
Sawdust created as a side stream of the mechanical forest industry is a suitable example. With regard to process development at LUT, the idea has been to utilise both the hemicellulose contained in sawdust and the energy content of sawdust. Hemicellulose can be processed into raw materials for certain products.
Potential applications with growing market potential are, for example, in the cosmetics, food and chemical industries.
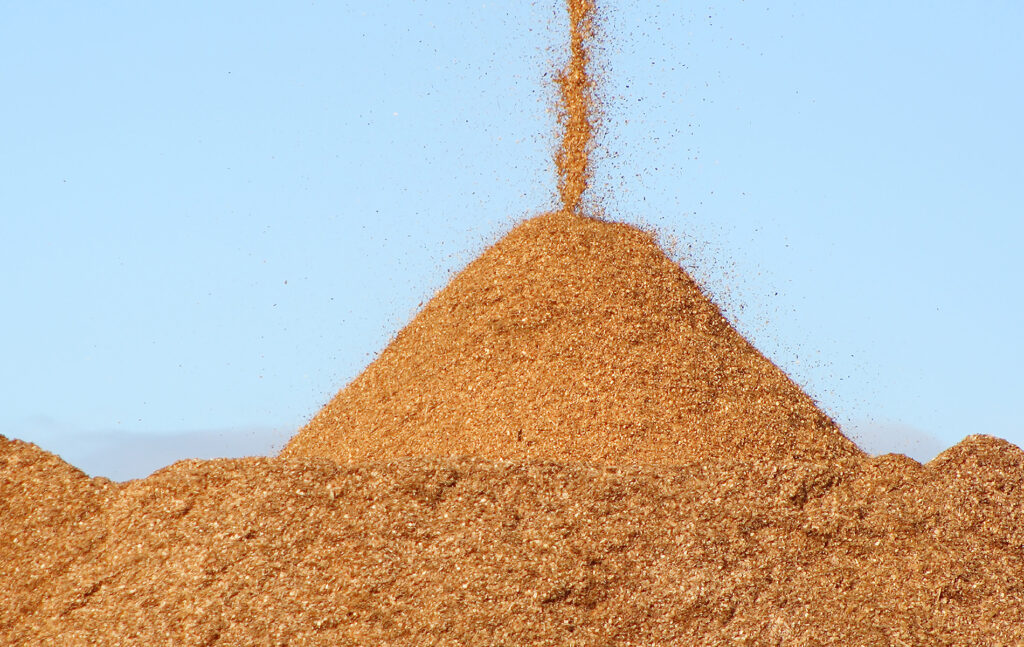
Insights and business risks
Raising the degree of processing requires product development, cooperation and investment. And risk-taking, as new products also need buyers.
“If you have a completely new product, it can be difficult to determine the market situation for it. Investments must also be made and production should be competitive and profitable. In addition, there are still oil and fossil-based products on the market that compete with your product.”
Kallioinen-Mänttäri points out that the green transition does not mean that the slate is clean and new products can just roll in.
“The old will live alongside the new for a long time. Bio-based solutions are not always the best. For example, plastic is difficult to replace with some other solution in certain applications.”
One thousand square metres for biofibre research
New product development is also in progress on LUT’s Lahti campus, where a biomass-based laboratory focusing on the research, testing and analysis of fibres and fibre products has been opened in close cooperation with Andritz Oy.
“This is a new kind of opening in Finland, as the university researchers and the company actively utilise jointly designed laboratory facilities. This allows for better interaction between the academic world and companies. We have a thousand square metres of research facilities in Lahti, where research related to fibre in particular is carried out. The laboratory’s fibre line and separation technology equipment also make it possible to develop the utilisation of side streams.”
It is good to remember that organisations are tasked with the practical side of things, people are.
“Researchers from universities and companies can work together. Knowing each other is also a prerequisite for successful research and product development.”
Long road from research to products
Kallioinen-Mänttäri emphasises one of the basic characteristics of research and product development.
“The time span is long. Many of the projects that are taking shape now have started with research at least a decade ago.”
When talking about innovations and product development, the development of production processes is easily neglected in favour of new product innovations.
“Processes lack the essential media sex appeal that new products have. Nevertheless, process development is essential for saving the water and energy consumption of facilities, for example.”
Kallioinen-Mänttäri presents another example of the importance of process development.
“When the treatment of wastewater from the coating colour kitchens of paper mills with membrane filtration became possible, it had a great effect on both environmental impacts and profitability. Thanks to the new process, valuable titanium oxide was recovered for reuse. It allowed for a very short payback period for the process investment, and both fractions from the membrane filtration could be directed to reuse at the factory. Instead of ending up as troublesome wastewater that needs special treatment.”